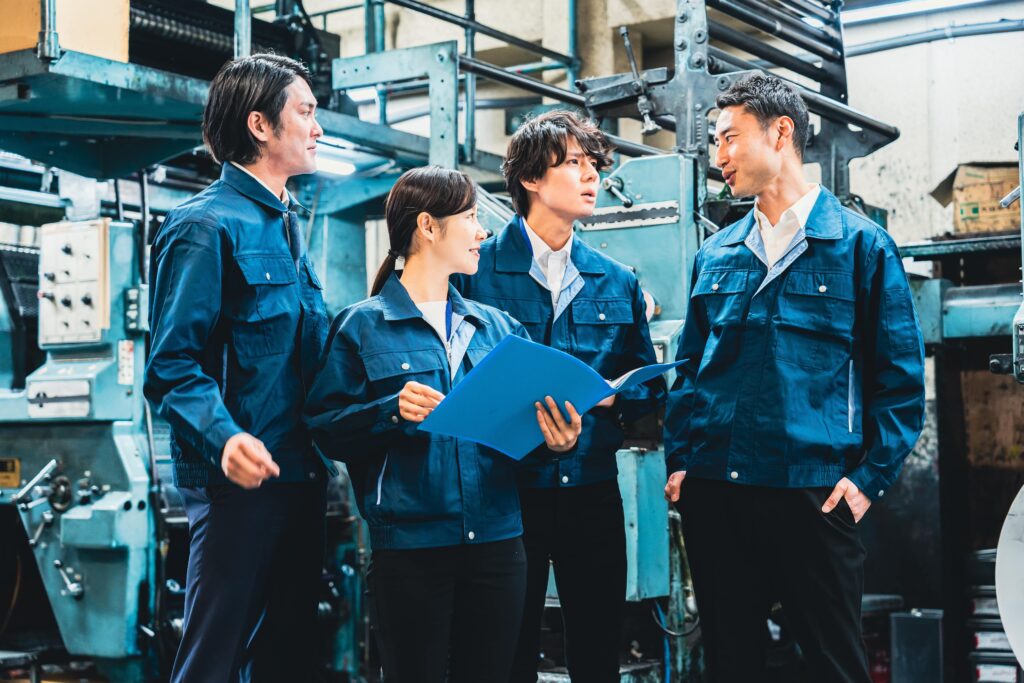
スマートフォンや電子機器の小型化・高性能化に伴い、接着剤や粘着剤などの機能性ペーストには、より精密な品質管理が求められています。秤量から混合、分散、フィルタリング、検査、小分けまでの各工程では、ディゾルバーや三本ロールなどの専門設備を駆使し、ミクロンレベルでの異物除去と均一性を実現しています。
機能性ペーストの製造工程とは?
機能性ペーストの製造工程は、秤量、混合、分散、フィルタリング、検査、小分け、脱泡という7つの基本工程から構成されています。最初の秤量工程では、フロアスケールを使用してSUSタンクに原料を正確に計量します。そして、エポキシ樹脂や硬化剤、各種添加剤などの液体や粉体を、製品仕様に応じた配合比率で投入していくのです。次の混合工程では、ディゾルバーと呼ばれる攪拌機を使用して原料を均一に混ぜ合わせます。
攪拌羽根とは逆方向に回転するターンテーブルにより、効率的な混合ができるようになります。分散工程では、三本ロールを使用して凝集した粒子を一次粒子まで細かく分散させます。
これにより、ペースト内の粒子のムラがなくなり、製品の品質が安定するのです。フィルタリング工程は、異物除去の重要な工程です。低粘度製品にはY字ストレーナーとポンプを組み合わせた装置を、高粘度製品には攪拌羽根付きふるいを使用します。
検査工程では、グラインドゲージによる粒度測定、粘度計による粘度測定、硬化性試験などを実施し、規格への適合を確認します。小分け工程では、クリーンルーム環境下でディスペンサーを使用してシリンジや各種容器に充填します。
最後の脱泡工程では、真空自公転脱泡機や遠心脱泡機を使用して、製品内の気泡を除去します。これらの工程を経ることで、電子部品の接着や回路形成に使用される高品質な機能性ペーストが製造されます。
混合と分散のカギを握るディゾルバーと三本ロールの技術とは
機能性ペーストの品質を左右する混合と分散工程では、ディゾルバーと三本ロールという2つの重要な装置が使用されます。ディゾルバーは高速ミキサーとも呼ばれ、攪拌軸の先端に取り付けられたタービン型ブレードを高速回転させることで、衝撃と剪断作用を発生させます。ブレード円周上のタービン状チップが、凝集した粉粒体を効果的に破壊し、液体と固体を均一に混合します。最新のディゾルバーには、回転数やトルク、モーターパワー、ディスクの周速などをリアルタイムでモニタリングできる機能が搭載されており、これらのデータはスケールアップ時の条件検討にも活用されます。
一方、三本ロールは、仕込ロール、中間ロール、仕上げロールの3本のロールが1対3対9の速度比で回転する装置です。ペーストはロール間の狭い隙間を通過する際、圧縮とせん断力を受けます。
これにより、凝集した粒子が一次粒子まで分散されます。ロール間隙は数十マイクロメートル単位で精密に調整され、最新機種ではポジションリピーター機能により、誰でも同じ隙間に再現性よく設定できるようになっています。
処理されたペーストは、速度の速い仕上げロールに転写され、ドクターブレードで掻き取られて回収されます。9インチや12インチの大型三本ロールには、チラー冷却システムが内蔵されており、分散時の摩擦熱による温度上昇を抑制します。
これにより、熱に敏感な材料でも品質を損なうことなく処理が可能です。ディゾルバーでの混合後に三本ロールで分散し、再度ディゾルバーでアフターミキシングを行うことで、粒子が均一に分布した高品質な機能性ペーストが製造されます。
異物除去で品質を守るフィルタリング工程の重要性
フィルタリング工程は、機能性ペーストの品質保証において極めて重要な役割を果たします。製造過程で混入する可能性のある異物や凝集物を除去することで、最終製品の品質安定性を確保します。とくに電子部品用の接着剤では、微細な異物が製品の詰まりや不具合の原因となります。そのため、徹底した異物除去が不可欠です。フィルタリングには、ペーストの粘度に応じて異なる装置が使用されます。低粘度のペーストには、Y字ストレーナーとポンプを組み合わせたシステムが採用され、連続的かつ効率的な濾過が可能です。
一方、高粘度のペーストには、攪拌羽根付きふるいが使用されます。この装置は、高粘度材料でも均一な濾過を実現し、メッシュの目詰まりを防ぎながら処理を行います。使用するメッシュサイズは、製品の用途や要求品質に応じて選定され、数十から数百メッシュまで幅広く対応します。
フィルタリング工程を適切に実施することで、ロット間の品質ばらつきを最小限に抑えることができます。これにより、顧客への安定した品質の製品供給が可能となり、製品の信頼性向上につながります。
また、シリンジ充填時の詰まりトラブルを未然に防ぎ、生産効率の向上にも寄与します。定期的なメッシュの交換と洗浄により、常に最適な濾過性能を維持することも重要な管理項目です。